Bastian Schäfer/Innovation Manager Emerging Technologies & Concepts
AIRBUS
Reading Time: 5 minutes
Ecken sind out – Airbus beschäftigt ein multidisziplinäres Team in einem Open Innovation Projekt um mittels Biomimicry unter Verwendung des Belastungsalgorithmus eines Schleimplizes die Kabinentrennwand eines Flugzeuges leichter und stabiler zu machen. Die Teile werden im 3D – Printing Verfahren gedruckt. Material ist eine Aluminium-Magnesium-Scandium Legierung um optimale Leichtigkeit und Festigkeit zu erhalten. Gewichtersparnis sind 30kg, die sich direkt auf die CO2 – Emission auswirken.
Was waren die Herausforderungen des Bionic Partition Projects?
Bastian Schäfer: Unsere Aufgabe war es, eine Kabinentrennwand – die Partition – für die Mittelstreckenjets der A320-Familie von Airbus zu optimieren. Die bisherige Bauweise besteht aus einem Metallgerüst, welches in Honeycomb eingebettet und mit CFK verkleidet ist. Die Partition muss einerseits stabil genug sein, um die „Cabin Attendant Seat Bench“, den Sitz, auf dem während des Starts und der Landung zwei Flugbegleiter sitzen, tragen zu können. Zusätzlich muss es möglich sein, einen Teil der Trennwand zu entfernen oder einklappen zu können, um im Notfall Personen auf einer Trage durchzulassen. Die Vorgabe des Projektes war es, das 3D – Druck Verfahren, bei Airbus “Additive Layer Manufacturing“ genannt, maximal auszunutzen, um auf diese Weise neue Designerprinzipien umsetzen zu können. Auf diese Weise konnten Strukturen generiert werden, die mit konventionellen Fertigungsmethoden bislang nicht herstellbar waren. Unser Ziel war es, das Gewicht der existierenden Partition um mindestens 30 % zu reduzieren. Nach heutigem Stand haben wir eine Gewichtsreduktion von 45 % erreicht. Die alte Partition wog 65 kg, die Bionic Partition wiegt nur noch 35 kg.
Die Gewichtsreduktion hat Auswirkungen auf die CO2 Emissionen?
Bastian Schäfer: Mit jedem Kilogramm, welches wir einsparen, verbrennen wir in den Triebwerken 106 kg weniger Kerosin pro Jahr. Nachdem wir 30 kg Gewicht reduzieren, können wir ungefähr 10 Tonnen an CO2 pro Jahr durch die Bionic Partition einsparen. Und das ist erst der Anfang. Wir können uns vorstellen, diese Technologie in Zukunft in unterschiedlichen Bereichen des Flugzeugbaues weiterzuverwenden.
Wie seid Ihr genau auf diese Trennwand gekommen?
Bastian Schäfer: Die Airbus Kabinenarchitekten haben uns hier in der Tat eine sehr komplexe Aufgabe gegeben. Die Trennwand muss extrem stabil sein, da sie im Zuge der Zertifizierung einen sogenannten 16 g Test bestehen muss. Das ist ein Crash-Test, bei dem innerhalb von 0,08 Sekunden eine Last von ungefähr 3,5 Tonnen aufgebracht wird. Die Lasten entstehen primär durch das Gewicht der Flugbegleiter, die auf der Flugbegleitersitzbank sitzen, welche wiederum an der Wand befestigt ist. Um hier zu einer neuen und gewichtsoptimierten Lösung zu kommen, haben wir ein Design umgesetzt, welches auf einem biologischen Organismus basiert. In unserem Fall nutzten wir einen Algorithmus, wie er beim Wachstum eines Schleimpilzes „Physarum“ vorkommt. Der Algorithmus liefert innerhalb eines „Generative Design“ Prozesses strukturelle Designs, die eher unkonventionell aussehen. Er hilft uns dabei redundante Strukturen aufzubauen, die notwendig sind, um die Lasten, die durch den Crash-Test entstehen, in die Primär Struktur des Flugzeuges einleiten zu können. Wir haben mehr als 10.000 Designvarianten durchgerechnet und haben mittels Big Data Analytics herausgefunden, welches das beste Design ist.
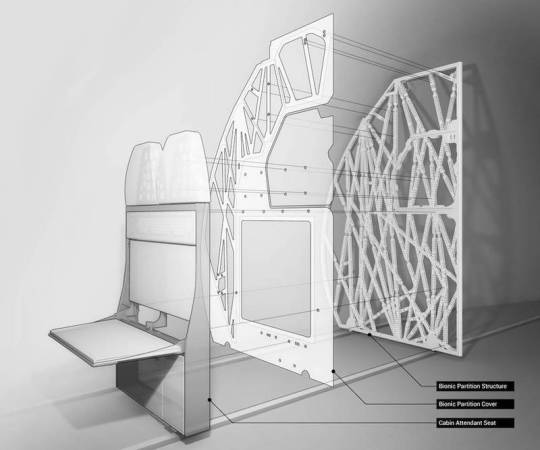
Concept Bionic Partition
Diese Biomimicry war eine Vorgabe oder ist es Zufall, dass der Algorithmus des Schleimpilz verwendet wurde?
Bastian Schäfer: Es war für uns naheliegend, dass wir den Schleimpilzalgorithmus ausprobieren wollen, da er zum einen bereits seit längerer Zeit beforscht wird und zum anderen redundante Strukturen generiert, die zu einer höheren Stabilität führen. Wenn einer der Lastpfade bricht, haben wir noch immer redundante Lastpfade zur Verfügung, die der geforderten Belastung standhalten können.
Welches Material verwendet Ihr zum Drucken?
Bastian Schäfer: Das Material ist ein neues 3D Druck fähiges Material von Airbus, basierend auf Aluminium-Magnesium-Scandium Legierung und welches unter dem Namen Scalmalloy™ bekannt ist. Durch einen kleinen Anteil von Scandium bekommt das Material sehr hohe Festigkeiten, welche höher ist als bei herkömmlichen Aluminium Legierungen. Teile des 3D Drucks wurden bei der Firma Concept Laser durchgeführt. Dort haben wir die Concept Laser M2 Maschine genutzt. Bei unserer Tochtergesellschaft APWorks ließen wir weitere Teile auf einer EOS M290 und einer EOS M400 drucken. Die EOS M400 gehört zu den größeren 3D Druckmaschinen, die es für den Metalldruck im Bereich des SLM Verfahrens gibt. In Summe mussten wir 116 Bauteile drucken und dazu 40 weitere Verbindungselemente aus Titan, um die Bauteile miteinander zu verbinden. Die additive Fertigung, mechanische Nachbearbeitung und Zusammensetzung von 116 Bauteilen sind für eine Serienfertigung leider suboptimal. Derzeit brauchen wir ca. 900 Stunden ausschließlich für den 3D Druck einer Partition, was deutlich zu lang ist. Die sich hieraus ergebenden Forderungen für den 3D Druck der Zukunft sind deutlich größere Bauräume der AM Anlagen, höhere Druckgeschwindigkeiten und eine Automatisierung der Nachbearbeitung, die derzeit noch den größten Kostenblock beim 3D Druck bildet.
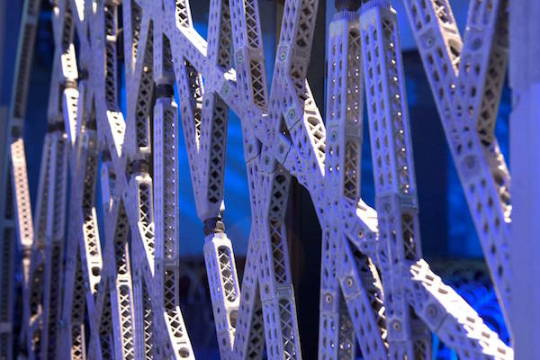
Partition Detail
Werden die Partitions schon in Flugzeuge eingebaut?
Bastian Schäfer: Wir sind derzeit in der Prototypen Phase und haben die ersten Partitions im 3D Druck Verfahren gefertigt. Diese wurden bereits getestet und die Ergebnisse aus den Tests fließen derzeit in die Weiterentwicklung ein.
Welche Entwicklungen erwarten Sie in den nächsten Jahren? Wird die Fertigungsindustrie revolutioniert?
Bastian Schäfer: Ich würde derzeit nicht von einer Revolution der Fertigung durch den 3D Druck sprechen. 3D Druck Verfahren haben mit Sicherheit ihren Platz neben den etablierten Fertigungsverfahren eingenommen. Positiv seien hier noch einmal die viel größeren Freiheitsgrade im Design genannt. Jedoch muss sich der 3D Druck weiterentwickeln, um auch Kosten technisch attraktiv zu sein.
Die Luftfahrt ist in einer Vorreiterrolle, da die verbauten Bauteile hochpreisig sind und das Thema Gewichtsreduktion im Kontext von CO2 Einsparungen als auch der Verbesserung der operativen Kosten eine entscheidende Bedeutung hat.
Wenn die Entwicklung so weiter geht, werden wir erleben, dass die Maschinen größer und schneller werden. Die Preise für den Pulverdruck werden sich verringern, sodass weitere Industrien davon profitieren können, und das nicht nur im Prototypenstadium, sondern auch in der Serienfertigung bei größeren Stückzahlen.
Die vielleicht größere Disruption liegt in den neuen generativen Designprozessen, die im Zuge dieser Entwicklung zunehmend Anwendung finden. Firmen, die es verstehen Designalgorithmen anzuwenden und selbst Algorithmen zu entwickeln, werden sehr erfolgreich sein. In Zukunft werden wir nicht mehr über eine reine Bauteiloptimierung sprechen, sondern über eine n-dimensionale Optimierung, die wir nutzen können, um unsere Produkte besser zu machen.
About:
Bastian Schäfer ist Innovationsmanager bei Airbus und erhielt 2006 sein Diplom an der HAW Hamburg. Seitdem arbeitet er für Airbus in verschiedenen Projekten und wurde schließlich ein Teil des Teams hinter der mehrfach ausgezeichneten Airbus Concept Cabin. Bastian ist Projektleiter des Bionic Partition Projektes, in welchem generatives Design mit dem 3D-Druck verknüpft wird.